CASE STUDY
UPPER LONGDON WINDMILL
The challenge facing designer Luke Bonwick and the construction team from Owlsworth IJP was how to design and build a windmill cap that was robust enough to support the workings of the windmill but still light enough to rotate freely on a “dead kerb” design. If the cap was too heavy, too much friction would prevent movement.
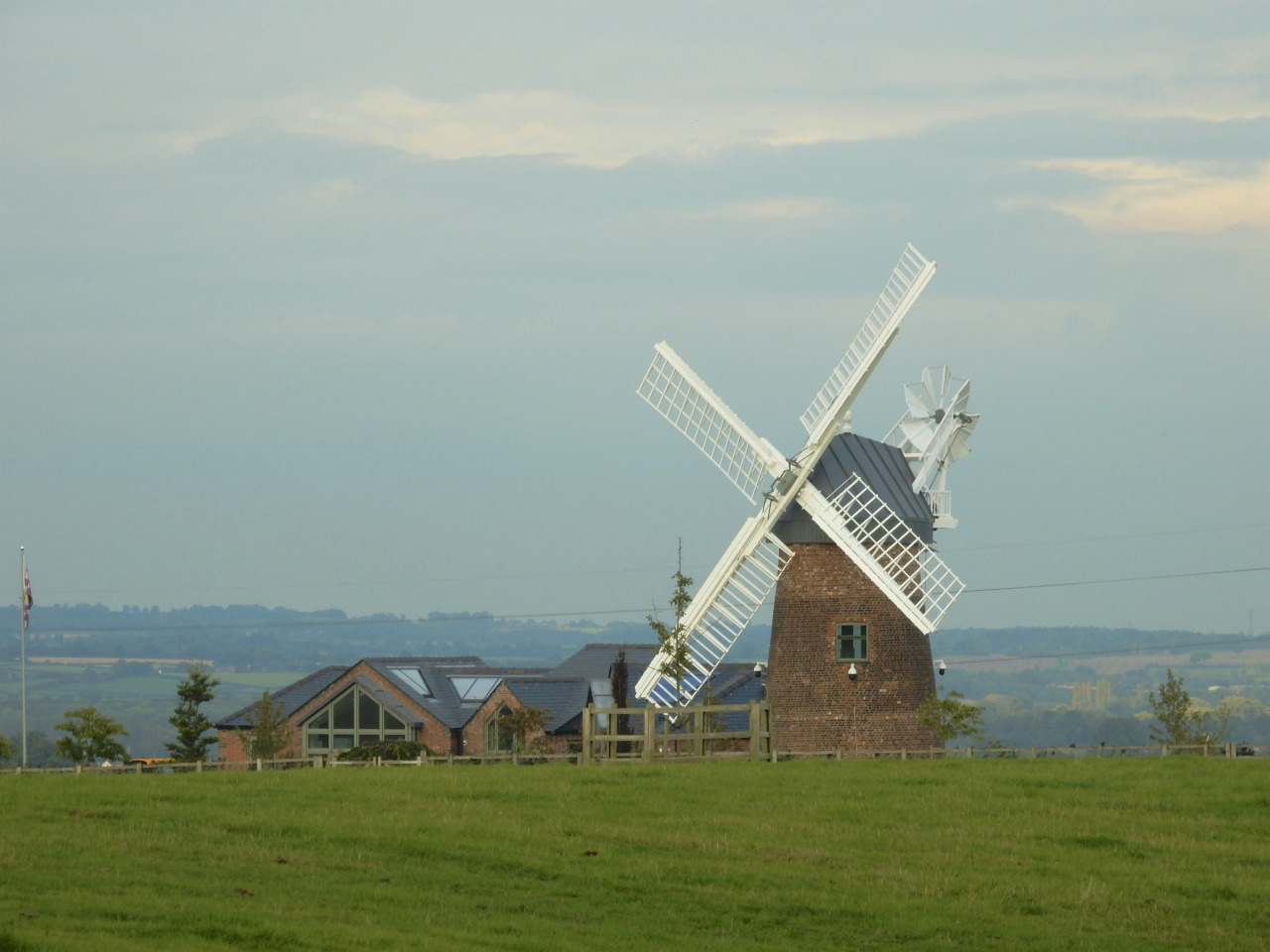
Details
Project name: Upper Longdon Windmill
Roofing Contractor: Owlsworth Roofing
Project Category: Small Project New Build
Project Location: Rugeley, Staffordshire. WS15 1QF
Material used: Sarnafil G410-15EL Lead Grey
Awards: Shortlisted for the Sika Sarnafil Small Project Award 2018
The challenge facing designer Luke Bonwick and the construction team from Owlsworth IJP was how to design and build a windmill cap that was robust enough to support the workings of the windmill but still light enough to rotate freely on a “dead kerb” design. If the cap was too heavy, too much friction would prevent movement.
With the oak structure already weighing in at a staggering eight tonnes, the concern was that with the additional weight of two tonnes of lead roofing materials the cap would simply be too heavy to rotate, leading to a catastrophic structural failure.
With the need to reduce the overall weight of the cap the team approached Owlsworth Roofing to investigate the possibilities of using single ply. Without the aid of any existing windmills weathered in single ply to work from, Owlsworth Roofing had to be sure that any solution would firstly, be viable and practical to install on the curved shape of the structure, capable of weathering the unusual details and penetrations that only a working windmill presents, and last but certainly not least, be aesthetically and commercially acceptable to the client.
Traditional flat roofing can be rather repetitive but in this particular case no two panels on any one side of the structure were the same size or shape. Fan spears would penetrate the roof at an angle on each side of the cap and the windward facing ‘head’ of the cap had the rather crucial element of the rotating wind shaft that carries the sails, passing right through the roof.
Owlsworth Roofing reached the conclusion that Sika Sarnafil could provide an answer to all of the questions that were being asked and the works commenced.
When working at height, the first question that should always be asked from a Health and Safety point of view is: “Is it necessary to work at height?” Usually, the roofer’s answer is simply yes – but on this occasion the answer was: “Not necessarily!” At least not for the majority of the construction works. The building of the timber structure and the first phase of the weathering of the cap was therefore carried out on the ground.
The cap was then craned onto the brick tower and the second phase of the weathering was carried out, which involved weathering a skirt over the joint between the cap and the tower to complete the roof covering.
Not all prototypes work at the first attempt, but Owlsworth Roofing’s use of Sika Sarnafil as a new and innovative solution to a traditional building concept capped off this project beautifully.